Asset Integrity Management
Risk Based Inspection (RBI)
For oil & gas, power and petrochemical installations, Risk Based Inspection (RBI) is a systematic approach to create an accurate,
well-targeted inspection strategy based on risk. The inspection plans are developed to mitigate the specific failure mechanisms identified.
We performs RBI study in compliance with standards API 580, 581, API 571. It is applicable to offshore & onshore installations such as
fixed or mobile units as well as FPSO's and pipelines.
Equipments include:
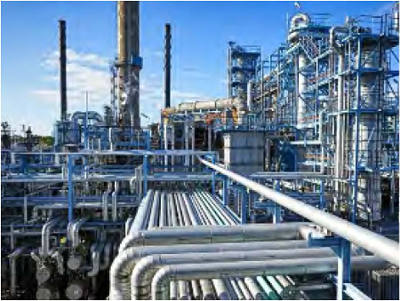
- Pressure vessels/drums
- Heat exchangers (shell and tube, fin fan)
- Columns
- Fliters
- Flare/stack
- Storage tanks
- Pressure relief devices
- In-plant piping pipelines
- Offshore structure
Reliability Centered Maintenance (RCM)
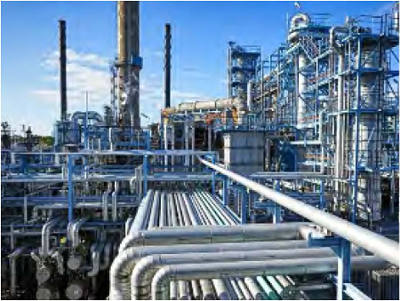
The RCM philosophy employs Preventive Maintenance (PM), Predictive Maintenance (PdM), Real-time Monitoring (RTM), Run-to-Failure
(RTF - also called reactive maintenance) and Proactive Maintenance techniques in an integrated manner to increase the probability that a machine or component will
function in the required manner over its design life cycle with a minimum of maintenance. The goal of the philosophy is to provide the stated function of the facility,
with the required reliability and availability at the lowest cost.
RCM requires that maintenance decisions be based on maintenance requirements supported by sound technical and economic justification. RCM study is performed in compliance
with standards BS EN 60812, SAE JA1011, SAE JA 1012, ISO-14224 & OREDA.
Our approach include:
- Screening analysis
- FMEA (Failure mode & Effect Analysis)
- Risk analysis
- Risk based maintenance (RBM) strategy development
Pipeline Integrity Management System (PIMS) (Onshore & Offshore)
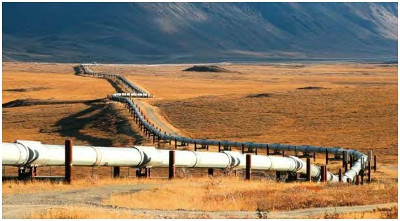
Offshore/Onshore pipelines transporting hazardous substances suffering consequences of poor integrity management have the potential to be catastrophic for the resident workforce on onshore/offshore installations and other users of the sea. An overview of the features and philosophy of Pipeline Integrity Management System (PIMS) highlights pipeline regulations and codes which are normally based on safety as well as risk philosophy. The Pipeline Integrity Management System program (PIMS) is developed for use by the pipeline engineers and for serving safety purpose. The design requirements are established so as to fulfill the objectives of the safety standards. The set of design criteria may thus be seen as the practical interpretation of it. Pipeline Integrity Management System is performed in compliance with international standards like API 1160, ASME B31.8S.
Safety Integrity Level (SIL)
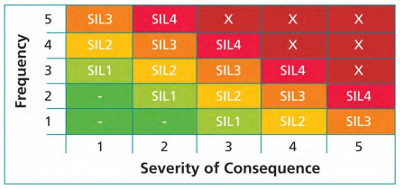
Safety Integrity Level (SIL) is the discrete level for specifying the safety integrity requirements of safety functions to be allocated to the “Electrical/ Electronic/Programmable Electronic Systems” safety related systems where SIL 4 has the highest level of safety integrity and SIL 1 has the lowest. SIL study is performed in compliance with standards IEC-61508, IEC-61511, ISA TR 84.00.02.
Reliability, Availability & Maintainability Services (RAM)
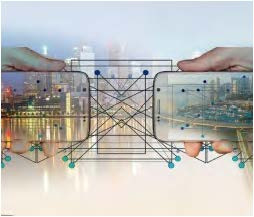
We provide detailed Reliability, Availability & Maintainability (RAM) analysis, to optimize a system by reducing the downtime, increase efficiency & optimize maintenance plans. RAM study is performed as per OREDA, ISO14224, BS-5760, BS-EN 61703, BS 4778-3. The ultimate purpose of RAM study is asset management; that is, running the system at maximum efficiency with minimum cost. RAM refers to three related characteristics of a system and its operational support: Reliability, Availability and Maintainability
Mooring Fitness for Purpose Assessment (MPFA)
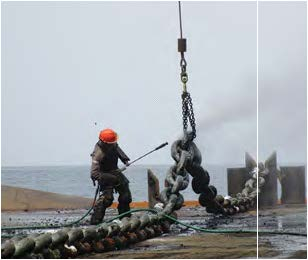
We are firmly committed to reducing risks and increasing safety in the offshore mooring chain through the provision of inspection and assessment intelligence that meets or exceeds industry best practice. Valintegs is also committed to providing its customers with high quality data and insight on safety critical subsea assets.
Wellhead Integrity Management System (WIMS)
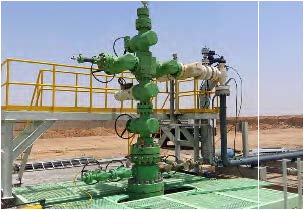
We use FMECA based RBI Methodology for Wellhead Integrity Assessment. The methodology is developed in accordance with BS EN 60812, IEC 60812, OREDA, API 6A, API 14B, API 14C, API RP 57 and ISOTS-116530-2 to optimize the preventive maintenance activities.
Structural Integrity Management System (SIM)
A structure can be designed to optimise functional buoyancy forces and hydrostatic pressure and to minimise the excitation forces associated with wind, wave, current,
seismic event and ice. Since the component member-sizes of an offshore/onshore structure, their configuration and arrangement directly influence the magnitude of these forces, they
are often defined as “dependent variables”.
We offer services of Structural Integrity Management System to ensure that:
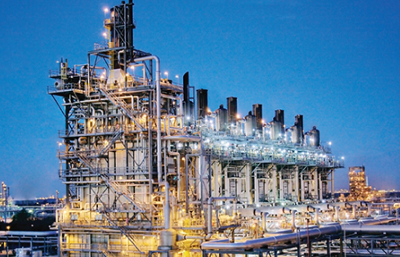
- The safety, environment and commercial risks associated with the operation of structures are identified and assessed.
- Appropriate risk reduction measures are identified, established and maintained.
- Risks to personnel, environment and business profitability are reduced to as low as reasonably practicable.
- Ensure that structural designs are ft for the intended purpose and engineered to approved standards.
- Assure the integrity of structures during all phases of their life cycle and assign single point accountability for this.
- Assure the integrity of structures during all phases of their life cycle and assign single point accountability for this.
RBI Methodology adopted for structures risk assessment is based on criteria provided in international codes ISO 19900, ISO 19902 & ISO 19904, API RP 2 SIM
We covers the following types of structures, as minimum:
- Offshore Platforms – Subsea Structures
- Offshore Platforms – Topside Structures
- Floating Production Storage and Offloading (FPSO)
- Onshore Structures